
Wed March 29, 2023
SBM Mineral Processing
For almost 40 years, SBM Mineral Processing has been consistently using diesel-electric drive systems and is a supplier of cross-technological hybrids for track-mobile jaw and impact crushers from under 50,000 to 350,000 lbs. operating weight.
Due to their sophisticated drive concept, the JAWMAX and REMAX plants rank at the top of their respective machine classes regarding crusher dimensions and production output without making any compromises concerning their mobility between sites or on the site, the manufacturer said.
Homogeneous Concept for All Types of Machines
SBM pursues a homogeneous concept for all of its plants to ensure the significant benefits of diesel-electric drive systems in all power classes. Depending on the market region, this also includes a plug-in option that enables the all-electric complete operation of the plants via mains power or external generators.
In addition to significantly lower on-site emissions in terms of exhaust gases and noise, all-electric operation brings considerable operating cost savings, the manufacturer said.
Parallel to the expansion of its global sales activities, SBM is working at full speed to make the plug-in option technically available in important regions, such as the North American markets.
The centerpiece of all hybrid electrified SBM mobiles plants consists of a diesel-generator-unit with emission-optimized Cummins diesel engines and directly flanged low-maintenance generators. The compact drive units are positioned outside of the dust-intensive machine zones.
As standard, the control cabinets are additionally overpressured and can be heated/air-conditioned for extremely difficult operations. In optional plug-in operation, the plant is supplied by the grid or by alternative external power sources (gen sets) at the control cabinet — activation is easy and safe by simply switching the central master switch before starting the plant.
From this moment on the central SBM plant control system Crush Control automatically starts, monitors and controls the individual machine components during crushing operations. Depending on machine type and equipment (scalpers, discharge conveyors, additional screens, etc.), up to 20 electric motors with a power input of 750 W (sprinkling) up to 250 kW (crusher) are used in the SBM plants.
The working hydraulics system (crusher gap setting, hydraulic cylinders, etc.) and the proportional traction drive are energized by two electrically operated pumping systems and circuits that are activated separately. This improves the energy footprint, for example by eliminating the unnecessary stand-by status of the track motors, and assures full functionality of the systems in all-electric operation.
In contrast to diesel-electric plants equipped with significantly more on-board hydraulics, SBM minimizes the oil quantities required on board to for example only 20 gal. compared to about 50 gal. respectively more than 160 gal. required by fully diesel-hydraulic models in the 40-ton class.
Instead of using complex hydraulic pipings meaning high thermal losses resp. costly oil cooling, all other drive systems and appliances in SBM plants are connected via break-proof cables, which practically eliminates environmentally critical leaks and corresponding breakdowns, according to the manufacturer.
Without the detour via hydraulic control blocks, electric activation ensures continuous quick response of the various plant components and facilitates easy and simple adaptation of feeding rates, screening capacities, or frequency-converter-controlled "extras" such as the automatic dedusting of chutes.
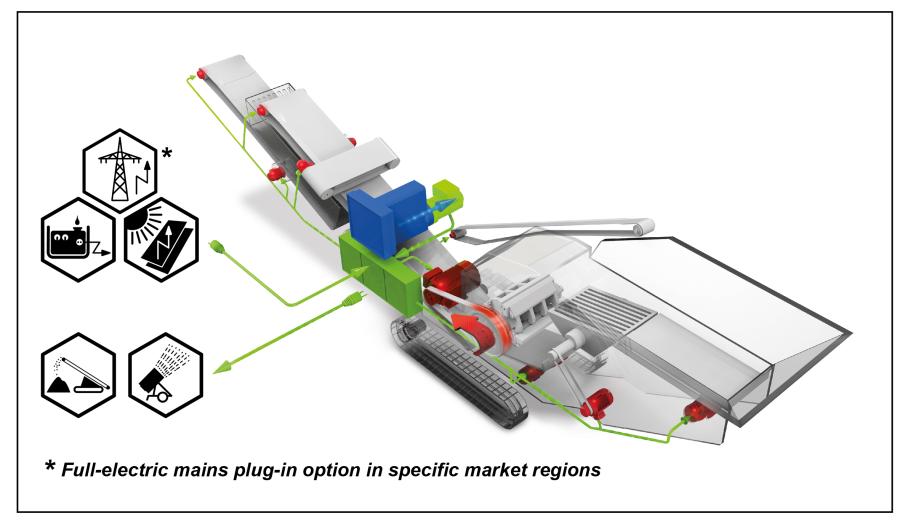
All SBM mobile plants feature a sophisticated hybrid drive system, available in many market regions with optional plug-in option for all-electric grid operation. (SBM Mineral Processing photo)
Efficient, Eco-Friendly
The degree of efficiency of diesel-electric drive systems can be considerably increased if energy-intensive hydraulic drive components are eliminated. At about 80 percent, the efficiency exceeds that of diesel-electric systems without or with optimized load-dependent control (ca. 40 percent / ca. 50 percent); and with grid connection the efficiency factor comes to more than even 90 percent. And this of course directly influences fuel consumption: The diesel engines of the SBM plants operating at a speed of 1,500 to 1,800 rpm adjustable in steps consume more than 40 percent less than all-hydraulic systems.
Compared to models with directly driven crushers, consumption is still reduced by 20 percent, the manufacturer said.
Given the sharp increase in fuel prices and in spite of varying electricity costs, it can be assumed that the 60 percent benefit in energy costs due to all-electric grid operation still rating as a rule of thumb has long ago further shifted in favor of hybrid technology. By now SBM anticipates that due to saving operational costs, diesel-electric hybrid plants with a high all-electric workload will — due to lower maintenance costs resulting from less wear and a longer service life — fully pay off even over a few years only.
With full flexibility in diesel-autarkic operation where SBM hybrids provide further environmental benefits on top of the reduced hydraulic volume and the consumption-based low emissions of their EU-stage-V-power plants: Thus, the elaborately enclosed diesel-generator units win over due to low noise emissions without load-dependent fluctuations. If switched over to all-electric operation, the noise generated by the same plant will decrease by another 6 dB significantly reducing noise emissions depending on geographical surroundings, the manufacturer said.
Even in all-electric "zero-emission" operation, possible effects on the immediate working environment are paramount: In tunnel construction or indoor recycling they are quite obvious, but for city-center demolition tenders technologies efficiently reducing exhaust emissions are becoming more and more important. This grants hybrid electrified plants a key competitive edge — not to mention the great image bonus of a company reducing its CO² footprint.
For more information, visit www.sbm-mp.at.
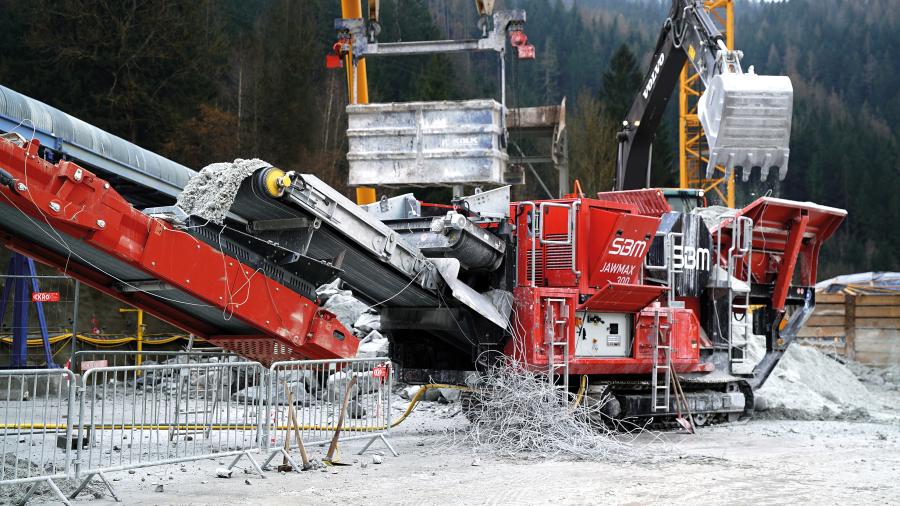
An SBM JAWMAX 300 with secondary screening unit in all-electric recycling operation. (SBM Mineral Processing photo)