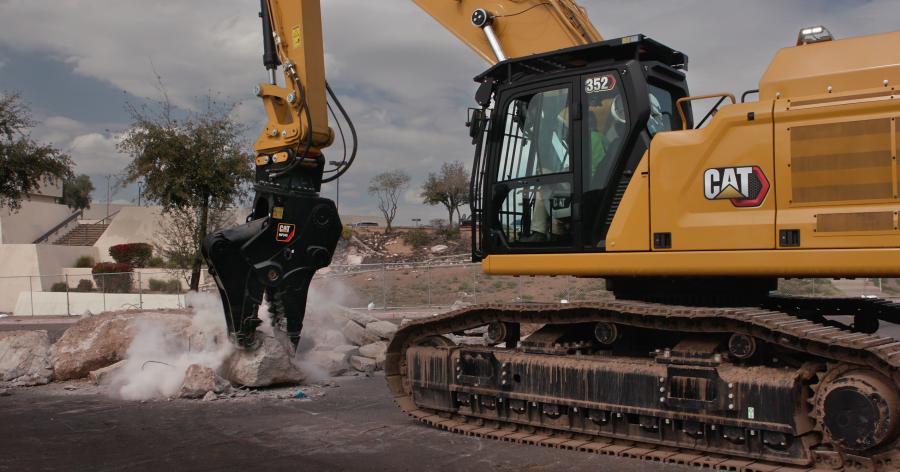
Thu February 23, 2023
Caterpillar
Built rugged for reliable operation in demanding applications, the new Cat 352 straight boom excavator is designed specifically for low-level demolition work up to five stories high, bridges and industrial infrastructures. Its stick/boom configuration delivers a higher vertical reach up to 42 ft. 2 in., 36 percent more stick pin height compared to the standard 352 Reach configuration.
Working with up to a 13,228-lb. attachment weight, the new 352 Straight Boom now features standard Cat technologies for increased versatility, precision and efficiency in both demolition and excavating applications.
The excavator's new optional 25,022-lb. removable counterweight design increases transportation efficiency and lowers transportation costs. The mechanical variable gauge undercarriage has a 9 ft. 10 in. transportation width when needed and extends 19 ft. 7 in. in working mode for maximum stability all around.
Its new high-efficiency hydraulic fan features standard automatic reverse to keep the cores free from debris and reduce maintenance time.
Simple, Safe, Reliable Operation
Designed for demolition, the 352 Straight Boom features reinforced booms, sticks and frame, increasing machine durability. Standard Falling Object Guards (FOGS) protect the roof and front reinforced P5A laminated windows from falling debris during demolition, while helping to maintain visibility of the job site.
Sloped to prevent mud and debris accumulation, the track frame design helps to reduce track damage, while sealed track pins and bushings reduce travel noise and help to increase undercarriage life. Full track guiding guard also is a standard feature
Its Operator ID function offers push-button engine starting and programmable joystick functions that are remembered when the operator enters their unique ID. Standard Cat Stick Steer simplifies excavator movements with single-hand and push-button operation of travel and turning.
Offering automatic power increase when needed, standard auto dig boost delivers better bucket penetration, shorter cycle times and greater payloads. Auto heavy lift offers more lifting power when needed for as long as needed. Cat Lift Assist makes the operator aware that the load is within the excavator's safe working range to avoid tipping
Standard Cat technologies to elevate operating efficiency include Cat Grade with 2D that displays depth and slope on the in-cab 10-in. touchscreen monitor. When excavating, Cat Payload offers real-time, onboard weight estimates to help achieve precise load targets. Payload can be combined with VisionLink for remote management of production targets, while Cat Product Link provides critical machine operating data like location, hours, fuel usage, productivity and diagnostic codes to help increase jobsite efficiency and lower costs.
To easily detect objects and personnel around the operator in a single view, the 352 Straight Boom comes standard with rearview and right-hand-sideview cameras, which can be upgraded to provide 360-degree visibility. Smaller cab pillars, larger windows, standard radial roof wiper and washer improves visibility around the machine. A premium seat, heated and cooled, is also standard.
Easily powering through all different types of material, the 352 Straight Boom features an electrohydraulic system and is powered by the field-proven 330-kW (443-hp) Cat C13B engine. Standard quick coupler, medium and high-pressure circuits increase operating versatility for using a variety of Cat demolition attachments. Three engine power modes — Smart, Power and Eco — help to match engine and hydraulic power to the task at hand to further reduce fuel consumption and costs.
Easy Maintenance
Harnessing technology, the new Cat 352 Straight Boom excavator now offers remote diagnostics and updating capabilities. Remote Troubleshoot allows the dealer to diagnose fault codes and machine issues remotely without interrupting the production cycle. Remote Flash allows software updates to be pushed out to the machine and installed at a time convenient for the customer.
Grouped together for simplified maintenance, all fuel filters now feature an extended, synchronized 1,000-hour change interval. Combined, these features help to lower long-term owning and operating costs.
Long-life fuel, oil and air filters reduce excavator time in the shop, and hydraulic oil checks and fuel system purging of water are done from ground level. The operator can easily track filter life and maintenance intervals from inside the cab. The updated hydraulic system improves filtration performance, while anti-drain valves help keep the hydraulic oil clean when replacing the filter.
For more information, visit www.cat.com.
This story also appears on Construction Equipment Guide.