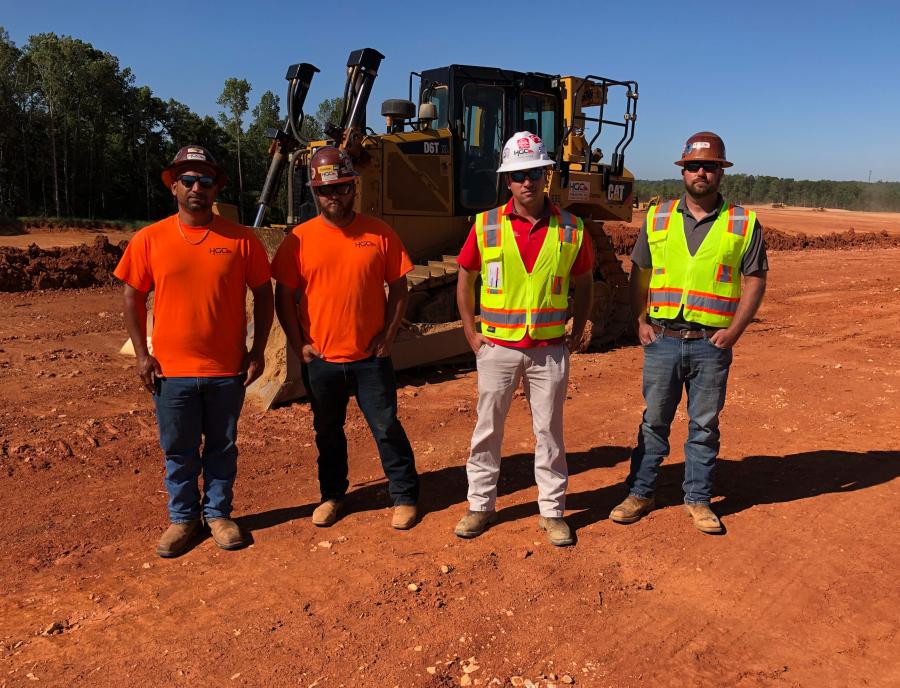
Thu July 21, 2022
Eric Olson - CEG CONTRIBUTING EDITOR
Over its almost 70 years serving the two Carolinas, Charlotte, N.C.'s Hoopaugh Grading Co. (HGC) has developed an outstanding reputation among contractors and developers for its prominent level of expertise in performing pre-construction work on projects of all sizes.
HGC was founded in 1953 and has grown to become a trusted and dependable specialist in site development across North and South Carolina. Its attention to detail, coupled with unparalleled customer service, has also kept its loyal client base repeatedly coming back.
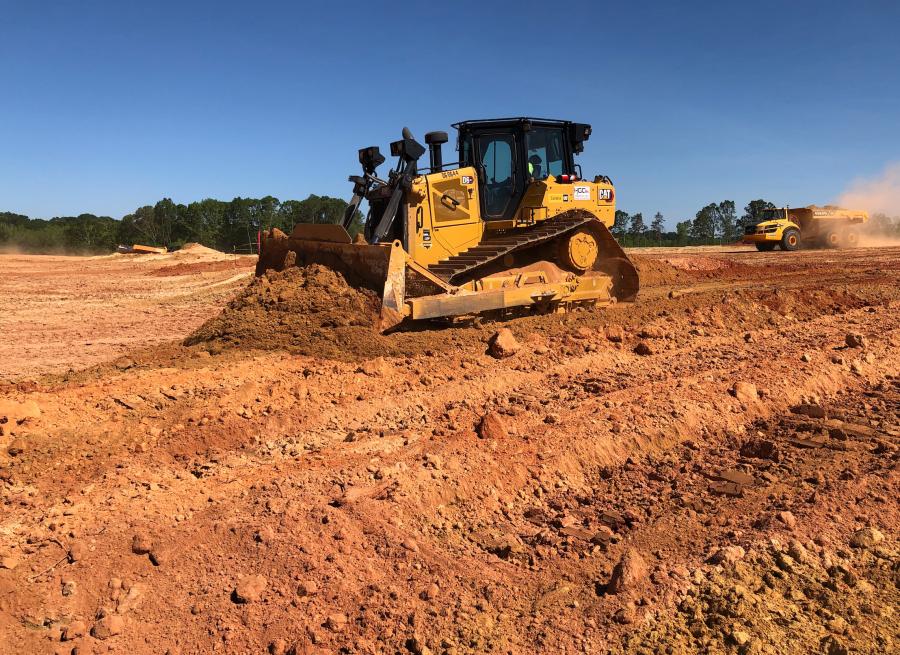
Word-of-mouth praise from happy clients also has brought more work its way, to the point that HGC is the company of choice in the region for site development.
That may have been what led the Silverman Group, a New Jersey commercial developer, to contract with HGC to ready 154 acres of a 200-acre site in the Rowan County, N.C. town of China Grove for the eventual construction of a 1.45 million sq. ft. Macy's fulfillment center.
The national retail chain, based in New York City, is expected to invest $584 million in the facility, located 35 mi. north of Charlotte off Interstate 85 at its intersection with N.C. Highway 152.
Macy's officials have said that when the facility is fully operational in 2024, 30 percent of the iconic retailer's online commerce will be shipped to and from China Grove. As many as 2,800 full-time employees are likely to be hired at the center, and Macy's expects to hire more seasonal workers around the holidays.
HGC to Finish Quickly and Efficiently
A ceremonial groundbreaking was held for the construction of the modern warehouse complex in late April, although HGC began clearing and grubbing the site in early January.
Stuart Hughes, the grading contractor's project manager at the Macy's site, said in the spring that HGC's work escalated from that point to now, despite having to work through a lot of wet dirt and a tight schedule.
In describing the task his company has taken on, he noted that his crews had approximately 1.7 million cubic yards of dirt to move to have to complete the building pad and turned over by the end of June. Once that was done, the general contractor could begin its work to stay on its own timetable begin.
"HGC is responsible for all the clearing and grubbing, site demolition, erosion control installation and maintenance, mass grading, fine grading, storm drain, sewer and water installation, segmental retaining walls, concrete curb and gutter, stone base, asphalt paving, and NCDOT roadway improvements," Hughes listed.
Equipment Big and Small Working at Macy's Site
To execute the site prep, of course, lots of well-built heavy equipment is needed, in addition to specialty tools to make the job easier. That includes excavators, dozers, off-road dump trucks, motor graders, and soil compactors. Lighter equipment on site at China Grove include GPS systems and drones.
"We are primarily managing the mass grading operations at the site with a combination of multiple large excavators and 45-ton articulated off-road dump trucks," he added. "Currently onsite we have five Cat 349 hydraulic excavators loading most of the dirt and 15 articulated off-road dump trucks, which are a combination of Volvo and Cat 45-ton vehicles."
Hughes explained that HGC prefers 45-ton trucks for their mass grading due to capacity and efficiency. Plus, these are the largest off-road dump trucks the company can move in and around the greater Charlotte area on short notice with an oversized/overweight permit using lowboys.
Likewise, HGC sees the Cat 349 excavator as hitting a "kind of the sweet spot for our set ups in terms of size and capabilities," he said.
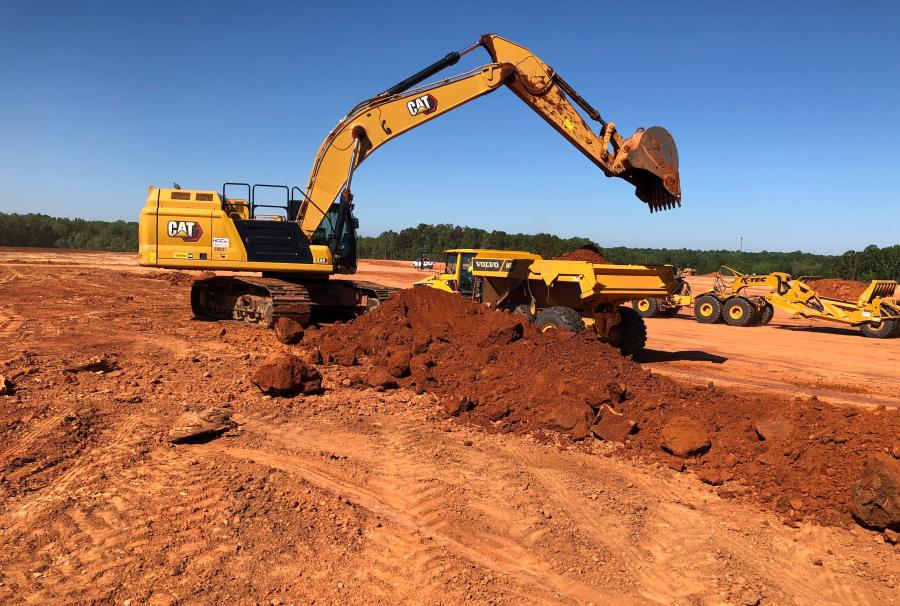
"The larger excavators have bigger buckets, but are not near as quick," Hughes continued. "Set up with the proper bench heights, we feel like we get the best cycle times with the 349s, paired with the 45-ton trucks."
HGC's dozers on the China Grove project include Cat D6Ts, three of which are used for mass placement of fills. There are also multiple Cat D6 XEs equipped with GPS systems made by Trimble, used for fine grading, and three Cat 815 soil compactors.
"We have one K-TEC 1237 ADT on site that we recently began using that can hold up to plus-or-minus 30 cu. yds. of heaped material," Hughes explained. "It is a 45-ton Volvo truck that pulls the pan and, on this project, has been able to load itself, which eliminates the need for four support machines and operators – two 45-ton trucks to haul, a dozer to push piles, and an excavator to load onto the off-road trucks. Compared to a 45-ton off-road truck hauling plus-or-minus 20 yards per load, the cycle time is also about half. In all, it has been moving more than 3,000 yards per day."
On HGC's best workdays, he added, the grading crews are hauling approximately 30,000 cu. yds. by using every piece of machinery on the Macy's development.
Hoopaugh Grading's in-house survey department, employing drones and GPS technology, also have played a key part in keeping the company on schedule at the massive China Grove site, Hughes said.
"We use drones to fly the site every two weeks to get an update on the latest site topography in reference to the proposed grading plans to see how much dirt we still need to move, and the magnitude of our remaining cuts and fills," he elaborated. "This data helps us keep a balanced site, which is an added benefit to our customers because it saves them money in hauling dirt to and from the project site."
According to Hughes, HGC's rolling fleet is currently made up of over 700 pieces of construction equipment. In addition, it has about 300 on road trucks and vehicles in operation.
Challenges Met, Overcome
When asked about meeting challenges to overcome at the site, such as negotiating through its rock and dirt, Hughes said the former has not been a problem.
The dirt, however, has been a different story.
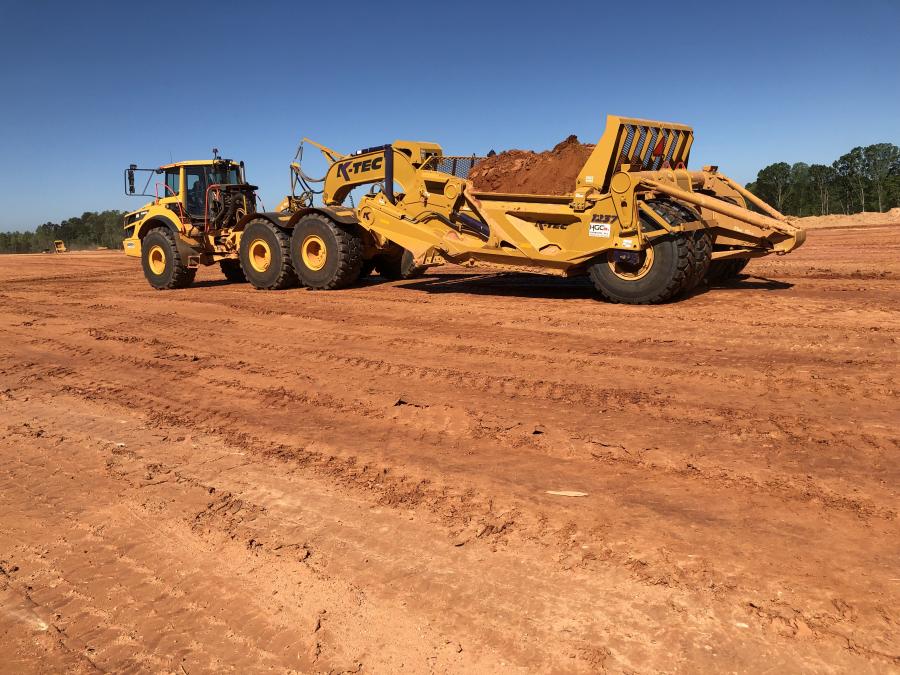
"The soil on this site has been extremely moisture sensitive, so after most rain events we have had to lime treat the soil to make it suitable to place and compact in order to keep the project moving forward." he explained. "To battle the wet soils, we have a soil stabilizer and a spreader truck onsite. A scale on the back of the spreader truck allows us to set the lime application rate evenly to spread where needed based on soil moisture contents, followed by the soil stabilizer that will blend the lime into the dirt, changing its chemical properties and making it a suitable fill for construction."
To stay on schedule, HGC began constructing the fulfillment center's building pad in late February by moving 600,000 cu. yds. of dirt just to get it on grade.
"Our field teams moved over a million yards of dirt altogether once we had installed the erosion control measures and ponds in order to allow us to get the pad on grade so the foundation contractor could start on the aggregate piers," Hughes added. "We stayed on schedule and were ready by the end of May], which meant that we moved all the necessary dirt in about 120 days to have the building pad turned over to the general contractor."
A Total Team Effort
HGC had as many as 34 people working on the Macy's project each day, he said, adding that much of the credit for keeping it a smooth-running operation goes to the site-development expertise of Steve Harper, the senior superintendent for HGC, and a pair of onsite grading superintendents in Taris Dial and Xan Cook.
"I cannot stress enough the talented teammates we have onsite, all of whom are important to our success," Hughes said. "It is all due to having the whole team show up every day to go to work and do their part safely and consistently. Each one is critical to the operation. For instance, if your excavator operator fails to show up for work and you do not have anyone there to load the trucks, the whole set is shut down. If a truck driver does not show, that lowers your overall efficiency and load count for the day, and without a dozer guy, we have one less machine there to blade roads, push piles, and fine grade."
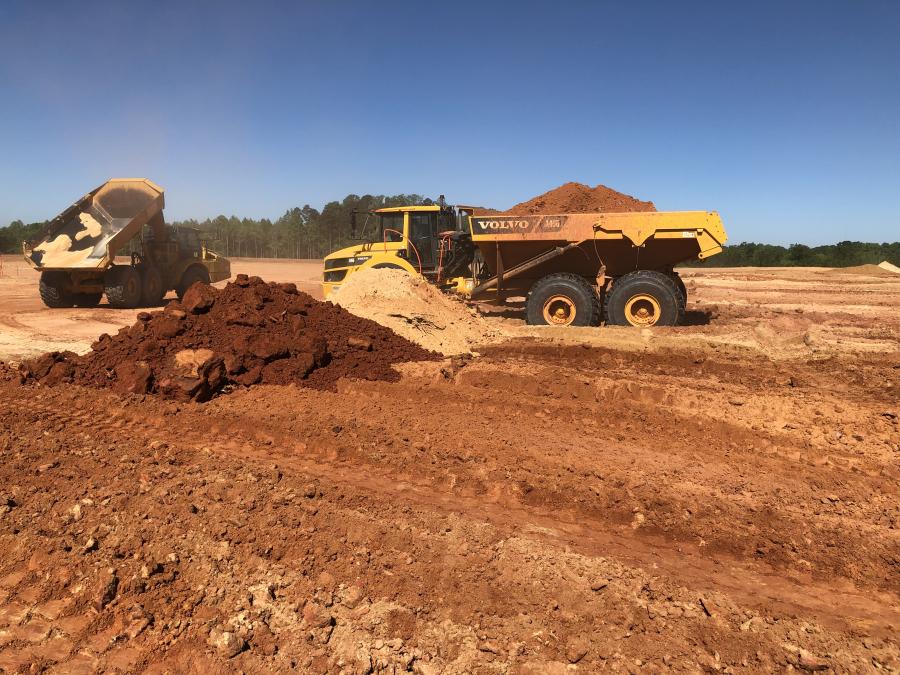
He also commends HGC's well-designed plan, path, and schedule, or PPS, for being able to keep the job running correctly and efficiently. An emphasis is placed on project staff meetings at regular intervals each week to plan and execute the work, always with an eye looking ahead to what is next.
"We have some of the best equipment in the business, thanks to Brian [McManus, owner and president of HGC] and the company's leadership group," Hughes said. "In the shop, we have the best mechanics to keep these machines moving. Our surveyors also are, I think, extremely critical to our daily operations. They are the ones that manage all the drones and complete all the topographic flights, do all our construction staking and layout, and record as-builts to make sure we are building the job correctly as designed. Every project starts and ends with them.
"The job of making sure we keep the project site clean and in compliance with local and state authorities is the job of Hoopaugh's erosion control crews," he described. "Our utility people make sure all the necessary storm, sewer, and water infrastructure is installed properly to keep the site flowing. In addition, the fine grade crews do a fantastic job of dressing up the site and placing stone base in preparation for curb and asphalt.
"It truly is a team effort to get these projects completed."
Young Project Manager Leans on Hoopaugh's Support
A native of Albemarle, N.C., about 40 miles east of Charlotte, Hughes said he has always had an interest in working in the construction industry, with a particular focus on sitework. During high school and later in college at UNC-Charlotte, where he graduated with a Bachelor of Science degree in Construction Management, he worked for a pair of other grading and utility contractors before joining HGC two years ago.
"[Hoopaugh Grading] is by far, one of the best sitework companies I have worked for because our leadership group gives us every resource needed to succeed on any project," he said. "We have layers of expertise available to us to get the answers to anything we need to know while on a project. It does not matter if it is a $30 million project or one that costs a half-million dollars, HGC treats all projects the same."
About HGC
Hoopaugh Grading Company, LLC (HGC) is a licensed general contractor specializing in turnkey site development in North and South Carolina. Established in 1953, it now employs over 675 office and field personnel with concentrations in erosion control, mass grading, fine grading, utilities, concrete, and surveying, as well as operations and safety training.
HGC has been listed as Top Workplace by the Charlotte Observer from 2018-21, and a Best Places to Work by the Charlotte Business Journal in 2019 and 2021.
For more information, visit www.hoopaughgrading.com/
This story also appears on Construction Equipment Guide.