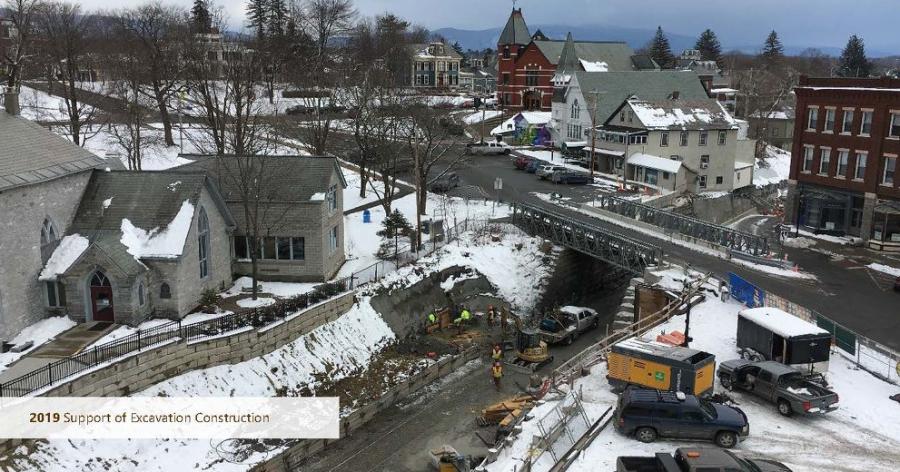
Thu March 24, 2022
Irwin Rapoport – CEG Correspondent
The Middlebury Bridge & Rail project, a Vermont Agency of Transportation (VTrans) initiative in collaboration with the town of Middlebury, is nearing completion this summer.
The more than $92 million project replaced two nearly 100-year-old bridges that crossed the Vermont Rail Corridor in the center of Middlebury with a tunnel in the summer of 2020. A 360-ft. long tunnel replaced the Main Street (60 ft. long) and Merchants Row (80 ft. long) bridges, which addresses several structural deficiencies.
Kubricky Construction Corporation (KCC) served as the construction manager and general contractor. The contractor was awarded three separate construction contracts over the duration of the project in order to advance critical items and maintain the overall project schedule.
The first contract was Early Work Package One, which was the removal of the existing bridges and replacement with two temporary structures. The second project was Early Work Package Two, which consisted of undergrounding utilities, construction of temporary infrastructure, drilling and blasting a 40-ft. diameter by 40-ft. deep launch shaft to be used for three micro tunneling drives for future drainage infrastructure.

The final construction contract was the main project, which consisted of temporary support of excavation, removal of the temporary bridges, excavation of the rail corridor, installation of the precast tunnels and U-walls, and then reconstruction of roadways, embankments and landscaping features.
The project is substantially complete and is awaiting completion and acceptance, which is anticipated to occur this spring. The remaining work is focusing on punch list items, such as final seeding, plantings and minimal general clean up.
"The tunnel provides vertical clearance for double-stack rail cars," according to VTrans. "By lowering the rail bed approximately 4 feet, clearance has increased to 21 feet without impacting the grade of the road and sidewalks above. The tunnel provides improved rail alignment, softening the rail curve to allow better horizontal clearance for trains. The project includes drainage improvements, mitigating the risk of icing problems as well as ponding that occurred historically."
The two bridges were about 300 ft. apart, with one located on Main Street/VT 30 and the other on Merchants Row. The structures were aging.
"For over 25 years, AOT bridge inspection reports documented ongoing deterioration of both bridges," said VTrans. "Concrete cracking, delamination and spalling had degraded all bridge components. Embedded steel reinforcement was rusted and exposed. There was leakage through the deck and full-depth holes on the Merchants Row sidewalk, requiring patching. In the spring of 2017, AOT became increasingly concerned about the deteriorated condition of the sidewalks and concrete that fell onto the railroad tracks. A sudden, unplanned emergency resulted in downtown Middlebury road closures for several months.
"The agency decided to replace both bridges with temporary bridges in the summer of 2017, until permanent structures were built," it added. "Both the Main Street and Merchants Row bridges were demolished and travel was restored within four weeks. [The] tunnel is a notable engineering and design feat within Vermont. After three years of construction, Middlebury stakeholders celebrated the process."
VHB is the Lead Engineering Designer for the project, which along with the AOT, balanced community needs and development character, local and regional mobility, construction feasibility "all while keeping the rail line active, except during the closure period," said VTrans. "Communities along the line depend on rail for deliveries of various commodities."
The project team, which consisted of the owner, designer, contractor and community liaison, worked out a plan that placed utilities in the Printer's Alley underground so that they did not interfere with crane operations for the tunnel construction; acquired right-of-way — temporary and permanent; negotiated with Vermont Rail Systems to secure work windows that enabled construction without interrupting rail service; monitored walls, foundations and windows of nearby historic buildings during activities that produced vibrations, as well as noise levels; found ways to mitigate a 100-year flood level of Otter Creek; ensured a design that considered community character and aesthetics concerns; created a safe working environment for workers, motorists and the community; scheduling a construction sequence to minimize community disruption; and developed a communication and outreach program to identify and respond to community concerns.
Replacing the bridges was considered, but VTrans noted that "the tunnel offers better safety, drainage and aesthetics. For example, it adds green space and connects Middlebury Village Green and Middlebury village historic district. Trains can now pass through town with less noise. The tunnel option was supported by the Middlebury select Board as it responds to the 2012 town plan to ‘close up the chasm that exists in the downtown area.'"
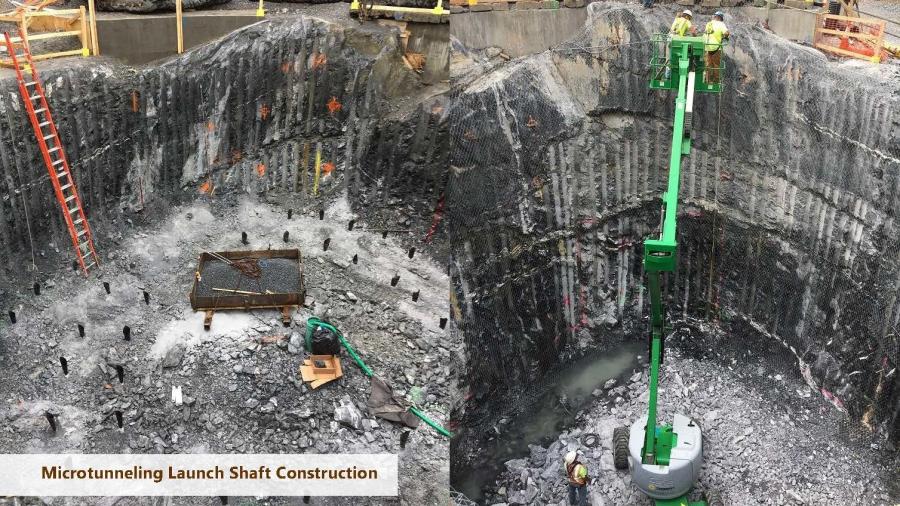
Prior to construction, the AOT conducted an environmental assessment in accordance with the National Environmental Policy Act. The project received broad support at public meetings and was endorsed by the Middlebury town select board.
The tunnel changes the town landscape by overlaying the depressed, walled rail bed with green space that links Triangle Park with the Village Green in the heart of downtown.
Aside from the 2017 Early Work Package One, which was the emergency replacement of the existing bridges and the 2019 summer road closures, the traffic plan is based on temporary road and lane closures where work is occurring.
The first permanent infrastructure work began in summer of 2018 with the first year focusing on micro tunneling, access roads and overhead utilities relocations. The second year focused on water, storm and sanitary utility locations and temporary support of excavation and preparatory excavation. The third year focused on the mobilization and stockpiling of material, bridge demolition, excavation, tunnel installation and roadways approach reconstructions. In 2021, activities focused on landscaping in Triangle Park, Village Green, and Lazarus Park and the reconstruction of Printer's Alley and final paving.
Last year's construction activities had crews installing new north and south cap walls, constructing berms and drainage swales along the southwest limits of the train tracks, reconstruction of Lazarus Park and Printer's Alley, landscaping and hardscaping in Triangle and Lazarus Parks.
Work was suspended during the winter months for between 2018 and 2019 (winter work did occur during the 2019-2020 winter season). During the summer of 2020, Main Street and Merchants Row were closed to traffic.
"Alignment of SOE was critical as we experienced some tight areas in terms of setting precast between lagging/sheet pile walls," said Bob Hyatt, Kubricky Construction's senior construction manager. "No conflicts were experienced, but it was close. Working through the COVID-19 pandemic with zero cases of infection throughout the tunnel construction was a challenge in addition to speaking very highly of the diligence of our personnel to remain safe and infection-free during shutdown. Coordination among numerous parties, agencies, subcontractors and citizens of Middlebury was challenging but also a ‘team' success story. All parties worked together to the point we created lasting relationships to all directly and indirectly involved."
Kubricky worked 24/7 during nine out of 10 weeks in the shutdown.
"No major utility issues were discovered throughout the project," said Hyatt. "KCC was able to acquire seven acres just outside of downtown Middlebury that became our storage yards for the precast and all aggregates and construction materials. Every involved party whether it was KCC, VAOT, town of Middlebury, all made it a point to work as a collective group to achieve the bridge opening date."
The temporary bridges were constructed in 2017 and taken down in 2020 over one week.
"The plan of attack was to take it out the same way it went in using a crane and excavator/dozer," said Hyatt. "The bridge was picked from its place and flown back to sit on the approach in order to later be dismantled. The challenge was creating the space to lay down the bridge for dismantling as well as coordination with the town/railroad."
The bridges were manufactured by Mabey and were made of steel members that were pinned and bolted together. They sat on precast concrete abutment slabs with a precast backwall to hold back the approaches.
The bridge was erected using a Caterpillar 307 excavator and telehandler, a Cat D4 dozer and a 100-ton Link-Belt crane. The approach work was installed using Cat D4 dozers.
Taking down the bridges was performed utilizing mechanical methods," said Hyatt, regarding the 2017 removal of the old bridges. "The challenge was protecting the tracks below while demolishing the bridges, as well as while hauling out all materials."
For the demolition of the Rail Tie bridge, the work was done via weekend shutdowns.
"The existing bridges were demolished and temporary bridges were set in place," said Hyatt. "This required us to close the road temporarily during construction, as well as perform all work over the railroad under temporary shutdowns. Railroad protection had to be installed during demo to protect the tracks, which required prior planning based on the time it took to set up and tear down. The other challenge was changing the existing approaches as the temporary bridge decks sat much higher due to the height of the beams compared to the existing bridges.
"Coordination with the railway was paramount to our success," he added. "Weekend shutdowns were provided, as well as windows of work during the week to perform everything."
The bridge decks were demolished with Caterpillar 335 and 307 excavators.
The tunnel construction required 10 week-long, 24/7 shutdowns.

"Previous weekend track closures were used to blast high bedrock in the north end of the tunnel," said Hyatt. "Additional blasting needed to happen during the 10-week shutdown itself beyond the Main Street bridge abutments. This work happened early in the shutdown and was a critical hurdle to clear to allow work to progress. A very tight work site in downtown Middlebury required a lot of coordination with local community and project stakeholders."
The erection of the tunnel began on July 24, 2020, and was concluded on August 18.
Prior to the shutdown, the work included: SOE — Installation of micropiles (~350 EA) and tie backs for upcoming excavation. Hundreds of linear ft. of temporary steel sheeting were installed in the northern section. There were several pre-shutdown weekend closures for blasting and utility pipe crossings.
"Utility work — storm, sewer and water improvements were made," said Hyatt.
The plan of attack, with the start of the shutdown, was to:
- remove the rail and temporary bridges;
- excavate down to grade while installing timber lagging on previously installed micropiles and grade and stone for precast;
- set precast tunnel, seal joints, grout bolt holes and backfill precast, and install retaining walls;
- pour new bridge decks, sidewalks and parapets, pave sidewalks and install tree cells and additional downtown granite curb and sidewalk; and
- eventually open to traffic with much other landscaping and hardscaping work to follow the shutdown period.
"This was a cut and cover tunnel and no tunneling machine was required," said Hyatt. "The rail corridor was excavated between micropile and timber lagging walls. The precast tunnel was assembled and then backfilled. Water trucks were on site to manage dust as needed as well as getting compaction when backfilling."
This work was equipment driven, with multiple excavators and loaders working as well as a Liebherr LR1300 300-ton crawler crane, two 200-ton crawlers and a 275-ton Link-Belt ATC-3275 hydraulic crane, and two Liebherr LR1200 200-ton cranes.
The road work required partial depth reconstruction of the bridge approaches, milling and repaving of the entire downtown area.
"We did not have a ton of challenges when it came to road reconstruction as the road was completely shut off from traffic," said Hyatt.
The road work had crews use a Caterpillar D4K2 dozer, a Cat 938M loader and a Dynapac CA150D roller.
The management team includes Construction Manager Nathan Speanburg; Project Manager John Whittaker; Project Engineer Ian Robison; and Field Engineers Grant Gilbert, Cassandra Mondello, Dustin Franke, Makayla D'Amore and Ben Pelchar. The superintendents included Roger Slater, Bill Hanchett, Cale Gleason, Pete
Olney. Forepersons included Al Matteson, Nick Popp, Nolan Diamond, Mike Shissler, Luke Herald, Addam Butler and Edward Allen.

"We had good comradery between the crews, especially during the setting of precast," said Hyatt. "Toward the middle of the precast operation, it became a friendly competition to see which crew could correctly set the most pieces in a 12-hour shift. It was a huge team effort. We had two 12-hour shifts rain or shine. There was lots of coordination and moving pieces. KCC crews, alongside our subcontractors, worked relentlessly and were able to complete the shutdown on time.
"Every morning at 6 a.m. we would have a handover meeting with the night crew," he added. "The day crew started at 7 a.m., so it gave everyone time to understand what was completed the shift prior and adjust the game plan if necessary for the day."
On peak construction days, there were anywhere from 50 to 70 people on site. Some of the main subcontractors are Engineers Construction INC (ECI); Maine Drilling & Blasting for drilling mini-piles and blasting into the rock ledge; Waters Excavation for sidewalk and curb; and Landshapes for landscapes and hardscapes.
Excavation operations within the rail corridor generated more than 26,000 cu. yds. of material, with some to be reused on the project, and 2,500 cu. yds. of solid rock removal, with the aid of Maine Drilling & Blasting.
"Soils in the project area have been thoroughly tested for the presence of contaminants," said Hyatt.
"A Corrective Action Plan was developed before construction began," said VTrans.
"We were able to reuse almost 7,600 cubic yards of material excavated from the rail bed in the non-contaminated areas," said Hyatt. "All the millings have been stored on site to be reused in future projects. Ashlar blocks were removed as the existing backwalls for the temporary bridges. These blocks were reused on site as park benches, as well as a component in the ‘rock core' berm that was constructed along Otter Creek on the southwest end of the project."
New construction materials included 210 cu, yds. of concrete for new bridge decks, 650 cu. yds. of concrete for new concrete cap wall and 3,500 tons of asphalt.
"Throughout the shutdown period we had a dedicated mechanic on call, as well as an onsite 8-foot x 20-foot container filled with any supplies or tools the mechanics needed that they did not already have in their vehicles," said Hyatt.
KCC purchases and rents equipment from Milton CAT in Clifton Park, N.Y., Contractor Sales in Albany, N.Y., and Chenango Contracting Inc. in Johnson City, N.Y. and in Middlebury, Vermont Champlain Valley Equipment, Champlain Construction and G Stone Commercial. CEG
This story also appears on Construction Equipment Guide.