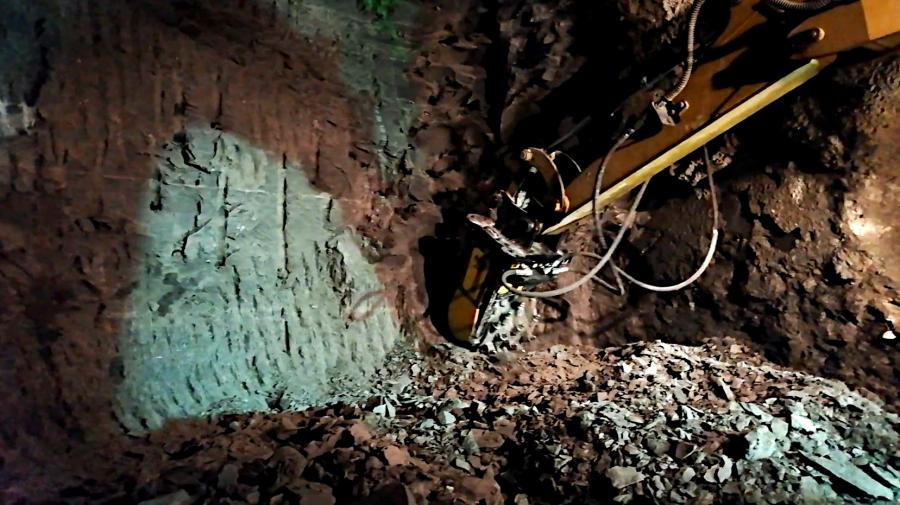
Tue July 27, 2021
MB Crusher
It's well-known that working in enclosed spaces multiples problems: it means facing challenges every day such as lack of access routes, little room to maneuver, managing incoming and outgoing trucks, managing materials and protecting workers.
As a result of the challenges, time and the costs of labor increase, which puts companies in a difficult position. However, there are available solutions: knowing what they are means opening your eyes to a new way of managing tasks with excellent results and turning expenses into a revenue source.
Hard to access areas and limited maneuvering room is no longer a problem
The most common challenges on construction sites in enclosed environments are hard to access and have limited maneuvering spaces. In quarries, tunnels, mines and construction sites inside factories or warehouses, managing incoming and outgoing materials are complex.
MB Crusher's attachments enter the tightest places and manage materials directly on site. The results are obvious: reduced waste, zero transportation costs and increasing the yard's profitability.
MB Crusher's entire range is designed to work even where space is limited because each product attaches to any brand excavator, even mini-excavators, turning them into a powerful crusher.
MB Crusher's drum cutters make it even easier to work in enclosed spaces. Making it the most effective solution to process only the material they needed with precision. Companies equipped with MB Crusher's units can independently recover and process waste materials, reduce costs and become more competitive, according to the manufacturer.
Extracting materials without explosives
Another critical point of working in enclosed spaces such as quarries and mines is managing the explosives and the workers' safety. In these situations, MB Crusher's units have changed methods and how profitable companies are.
For example, in a mine in Albania, extracting iron-nickel happened using explosives, which comes with the costs of the explosives and the safety measures. None of the operators were aware of an equally effective alternative method.
By inserting MB Crusher's units, they abandoned using explosives, and extraction happens with the MB-R700 drum cutter installed on an 18,000 lb. Bobcat 442. A drastic change for the company and also the entire sector.
The same attachment has been used in many quarries and mines, solving the problems surrounding using explosives for extraction.
Furthermore, MB Crusher's drum cutters are an effective answer to mill only the necessary material without generating waste material that they need to dispose of. They also avoid creating dangerous vibrations if they work underneath roads, excavations located in cities, or inside industrial warehouses close to other buildings.
In Mexico, as a recent example, for them to build a drainage tunnel underneath a busy road, they couldn't use a hammer since it would have created too many vibrations. However, an MB Crusher MB-R500 drum cutter installed on a mini-excavator solved the job without creating vibrations or cracks in the walls — they only processed the material they needed.
Immediate operational and economic benefits
The units from MB Crusher's range present a turning point for organizations working in enclosed spaces to become faster and economically advantageous.
Let's look at an example of a job in South Tyrol in Italy, where an industrial warehouse's floor had to be dismantled and redone. By inserting a BF120.4 crusher bucket on the Doosan excavator present on site, all of the inert material was crushed on-site and used to create the new layer for the new flooring.
Easy to install and operate, MB Crusher's attachments transform any material into a resource, even enclosed environments or on construction sites that are hard to access. With its products, MB Crusher has revolutionized the process and turned construction sites into autonomous crushing centers that yield excellent performance and increase profitability, the company said.
For more information, visit www.mbamerica.com.