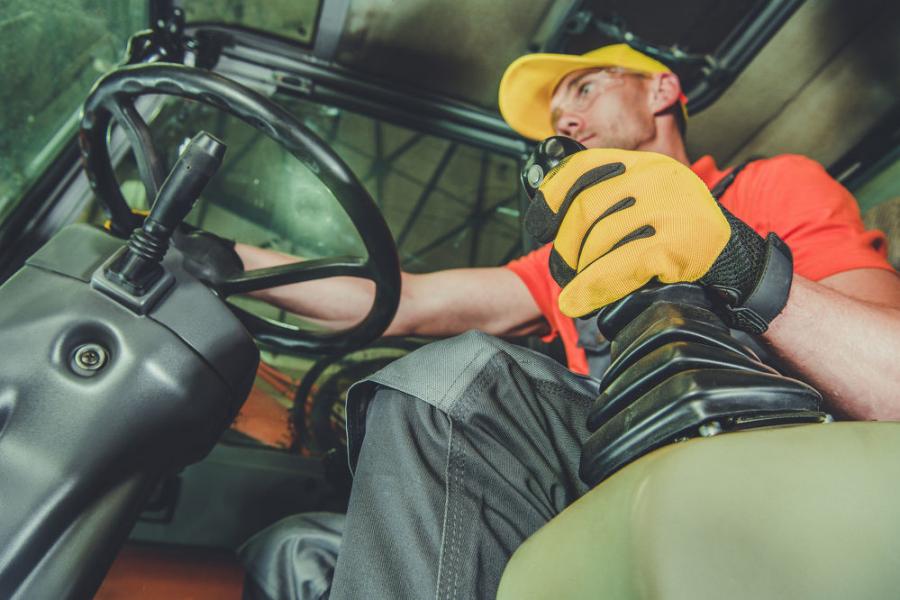
Thu June 18, 2020
Lucy Perry – CEG CORRESPONDENT
Implementing new technology into construction is a smart decision, but it's a process. The technology must present tangible value from Day 1, and it has to make sense for the job site. It must work as well in the field as it did at the tradeshow. Smart contractors choose products or platforms with the worker in mind.
Peter Maglathlin, CFO of Trade Hounds, an app and social network that connects U.S. construction workers, said "a product or platform that is geared toward the worker, not management, will be most widely adopted and engaged with, and therefore have the most impact."
Three types of smart data collection technology trending in the construction sector right now — drones, wearables and machine automation — are moving the industry forward in a big way. Contractors who have put these tools into the hands of their employees are seeing success in the field through increased safety, efficient operations and higher productivity.
Providence, R.I.-based construction company Gilbane Building Company has successfully integrated wearables technology with Triax Technologies' Spot-r wearable device. Lori Peters, vice president of marketing for Triax, Norwalk, Conn., said Gilbane adopted Spot-r as a way to support their safety culture.
"They are providing their workforce with a tool that enables them to take ownership of site safety and contribute to the site safety culture."
Safety on Your Sleeve
Wearables fall into three categories. Visual wearables use optical aids in or on glasses, visors and hard hats to produce images. Tactile wearables increase the user's strength and durability via an exoskeleton. Sensing wearables detect conditions, analyze data and warn the employee of hazardous situations
Triax Tech's Spot-r device provides contractors with real-time data on jobsite access, worker and equipment location, manpower, safety incidents and evacuation and muster procedures.
"Every worker is regularly trained to utilize the Spot-r push button to report injuries, incidents and hazards," said Peters. "They've been able to improve their injury response time by 91 percent.
"They are also utilizing our points of interest solution to identify if workers are accessing hazardous or restricted areas and Spot-r EvacTags to enhance their evacuation protocols and monitor evacuation procedures in real time," she added.
One of the newest trends in wearable technology, specifically in response to COVID-19, centers around proximity alerts and digital contact tracing, said Peters. The company's Proximity Trace tags can be mounted on a hard hat or worn on the body to alert workers with a visual and audible alarm when they are in close contact with another worker.

"This is very effective in reminding workers to adjust their current distance to a proper social distance of six feet or greater," Peters said. "Additionally, each of these close contact interactions are passively collected and transferred to our cloud-based dashboard to facilitate contact trace reporting should a worker become symptomatic or test positive for COVID-19."
Wearables are one avenue by which smart technology has become more visible on job sites. The technology is improving the amount of automated, real-time information contractors have access to, enabling them to respond and react to the data to drive safer, more productive job sites, according to Peters. Contractors gain actionable insights to streamline processes, and improve safety and productivity, she said.
Another aspect of productivity, she added, is to see where the equipment that contractors need to be productive is located.
"A lot of times we hear, ‘I needed a scaffold' or ‘I needed some kind of a scissor lift and there weren't enough on site,' when in fact, a jobsite supervisor can see where that equipment is located because we can tag it."
Higher Visibility
A clear picture of job sites, equipment and crew is what many contractors boil the usefulness of drone technology down to. But aerial photography just touches the surface of how the remote devices can be used.
"Most general contractors know they have to be using drones on job sites," said Andrew Wolfe, pilot-in-command of Drone Brothers, an aerial photography service based in Troy, Mich.
"If you asked them, 99 out of 100 general contractors and project managers would say ‘Yes, they're great for taking pretty pictures of a job site.' But I see their jaws drop when I talk with them and they realize, ‘I didn't know drones could do that. XYZ project would have been a perfect site for that.'"
In early construction phases, drones not only aid in site selection, but also can chart site conditions before construction equipment is brought in. Wolfe said clients will document road conditions and structural locations to meet the requirements of local governmental entities. After equipment is staged, project progress is monitored on a daily basis with the device.

"What drone technology is getting better at is we can get where we want to go for shots of high-traffic areas," Wolfe said. "We can also tell the drone to go from corner to corner of the site and capture 15, 16 photos from the exact same location for consistency every time the pilot flies. So, when the project manager is looking at the reports, he's used to seeing the same angles and pictures all the time."
He said a drone pilot can instruct the drone to go to a certain location and take photos of all angles from the same spot. The result is a panoramic view of the site captured from moments in time. Drones also can fly the site and shoot 15 or 20 minutes of raw video footage. Back at the office, the best 90 seconds of footage can be captured to highlight what's going on at the site.
"Videos can then be personalized with the client's logo, a date stamp of when it was taken, and the name of project for their clients," he said. "It can then be used as a marketing tool."
Drone Brothers client, Kansas City, Mo.-based Ryan Companies, likes to see a daily birds-eye view of the project site under construction. Another Drone Brothers client in Iowa uses the drone's mapping feature to overlay a site plan to see if structures on the site are lining up properly.
"They want to know if a certain tree is still standing or has been removed, or if power facilities are linking up," said Wolfe.
"From a reference point, they can determine what is planned versus actual activity," he added. "They can take our map and overlay it on their site plan. This client has an 80-inch computer monitor in a trailer. The site is over 150 acres, and they bring our map up on the monitor. They can walk up to the map, point out where materials need to be stacked, why structures are still standing. They can communicate what's going on at the site with the entire construction team."
Another client in Albuquerque, N.M., used a drone map to track prefabricated curbs which were missing from a job site.
"They were supposedly delivered on a certain date, but the client never got them," said Wolfe. "The day after, we'd flown the site. They used our map to share with the people who were supposed to deliver that the curbs were not there. They were able to document that with drones."
Tracking materials is another big benefit of drone technology, he said. The devices can be used to measure stockpiles.
"Drones can do what it takes a surveyor days spent measuring crushed rock, for example. We can do the same with a drone with plus or minus 5 percent accuracy in hours rather than days."
Drones can also be used in site inspections. The technology is getting so sophisticated the user can build a 3D model of the project site. The drone can go around a building, take thousands of pictures, and stitch them together, zooming everything into one picture.
"We're virtually taking the computer and moving it where you want in a building, clicking on a window ledge and the software zooms in further to see if there are cracks or breaks on the molding," said Wolfe. "We're building 3D models of the building in order to zoom in and inspect. The software allows the user to drop in comments or ideas to share with team."
Machines With Smarts
Automated machine control is smart technology that helps prevent problems on the off-highway construction site. One example is Komatsu's intelligent Machine Control (iMC) version 2.0, introduced at ConExpo in March.
"No longer does an operator need to look to a grade checker/laborer or ground stakes for guidance on where to move the earth," Komatsu's website explains. "Now, 3D design data is fully integrated into the machine and the operator is guided to work at high efficiency."
These machines control the blade and bucket with sophisticated automation, aligning material movement to design decisions. The iMC 2.0 suite is designed to increase dozer productivity.
Features include proactive dozing control that automatically cuts and strips from existing terrain like an experienced operator. It automatically spreads fill from existing terrain; tilts the blade to maintain straight travel during rough dozing; and creates a temporary design surface with one press of the button.
The technology, said Chris Potter, technology solutions expert of Komatsu dealer Road Machinery and Supplies, Savage, Minn., is helping contractors get to grade faster with less-experienced operators.
Road Machinery & Supplies Co. offers customers Komatsu iMC equipment with integrated GPS technology, propeller drone and software mapping services, GPS training, and iMC demo events.
"Help is one of the biggest challenges contractors face currently," said Potter, referring to labor shortages in the construction industry. "The technology is helping contractors eliminate guys on the ground, and since the machines are more productive it can [eliminate the need for] extra equipment on site."
An operator can excavate a footing without a second person on the ground. The contractor can eliminate a dozer out of a sub cut because the excavator is getting that cut on grade.
"Traditionally, this would be an excavator and dozer project, but now the dozer can focus on other parts of the job or not be there at all," he noted. "Proactive dozing control is increasing the productivity of seasoned operators" who now can use the automatics from rough cut to finish grade, he explained, adding that the technology has been used on just about every task in the field.
"Street reconstruction, new developments, underground utilities, parking lots, building footings, athletic fields, farm drainage projects — the list goes on and on. We have sold machines to customers that have two employees." Potter believes the technology is essential for off-highway contractors.
Upgrading the Job Site
"You are really behind your competition if you are not utilizing the technology," said Potter. "Having been with a contractor for 11 years and having field experience I cannot think of a task where it could not be utilized."
In fact, many people would say the same of smart technology in general on construction sites. As San Francisco, Calif.-based field data platform developer Rhumbix points out in a blog post, technology in construction is revolutionizing almost every aspect of the business.
"If you haven't yet, it's time to adopt some of the new technologies driving construction forward. They'll help you keep pace as your company benefits from industry growth." CEG
This story also appears on Construction Equipment Guide.